Special methods
Drilling is essential not only for piles, but also for anchors, wells, geothermal heat or injections. These special methods require their own unique procedures and equipment.
Anchor drilling
Anchors are used to safeguard retaining structures, for example. They support the side walls of an excavation pit so that they do not give way under the load generated by the earth pressure – the tie-back of a retaining structure makes struts unnecessary. A ground anchor consists of three main components: the anchor head, a free anchor length (steel tendon) and a force application length that is connected to the construction soil by a grout body. During anchor construction, the steel tendon of the anchor is inserted into a bore hole. The bore hole is pressed with bentonite in the area of the force application length. After the cement hardens, the anchor is tensioned with a stressing jack from the free end. Then the strands are fixed in the area of the anchor head.
High pressure injection (HDI)
The HDI method is used for underpinning or strengthen the existing foundations, to close gaps, for high and low-lying bases, as a screen injection in tunnel construction and for the fabrication of cut-off walls. The underlying principle: A drill string is inserted into the ground using a drilling rig. At the bottom end of the HDI drill string, there is a nozzle on the side that injects a fluid (water or binder slurry) under high pressure (400-600 bar). The high-energy “cutting jet” that is generated loosens the soil from its natural position and displaces it with binding agent. By turning and pulling the HDI drill string at the same time, the cutting jet traces a tight spiral in the soil, thus creating a columnar cavity. This is filled with binder slurry and soil. The binding agent hardens the mixture to produce a sturdy HDI column.
The advantages of this low-vibration method include
- High safety due to construction before excavation,
- Application under tight spatial conditions and restricted working heights and
- Nearly unlimited drilling depths.
Exploration and water well construction
BAUER RB rigs can be used for numerous drilling methods (with optional special equipment as needed and depending on the geological conditions);
- Air lift drilling method
- Other reverse circulation drilling methods (e.g. suction drilling)
- Direct pressure flush drilling
- Rope core drilling
- Ram core drilling
- Down-the-hole hammer drilling
- Dry rotary drilling (auger drilling)
- Drilling with rotary casing table
With the air lift drilling method, blowing in air generates an upwards movement in the drill string which transports the mixture of a water-based drilling fluid and drilling fluid to the surface. After the separation of the drill spoil and drilling fluid, the flushing fluid flows back into the bore hole. This method is used for water well construction, mining (e.g. drainage walls, mass sampling, ventilation shaft drilling), for pre-drilling to install anchor casings for deep geothermal energy, and in the area of crude oil/natural gas. Particularly for large bore hole diameters (> 300 mm), this drilling method is considerably more efficient because no large flushing pumps are required.
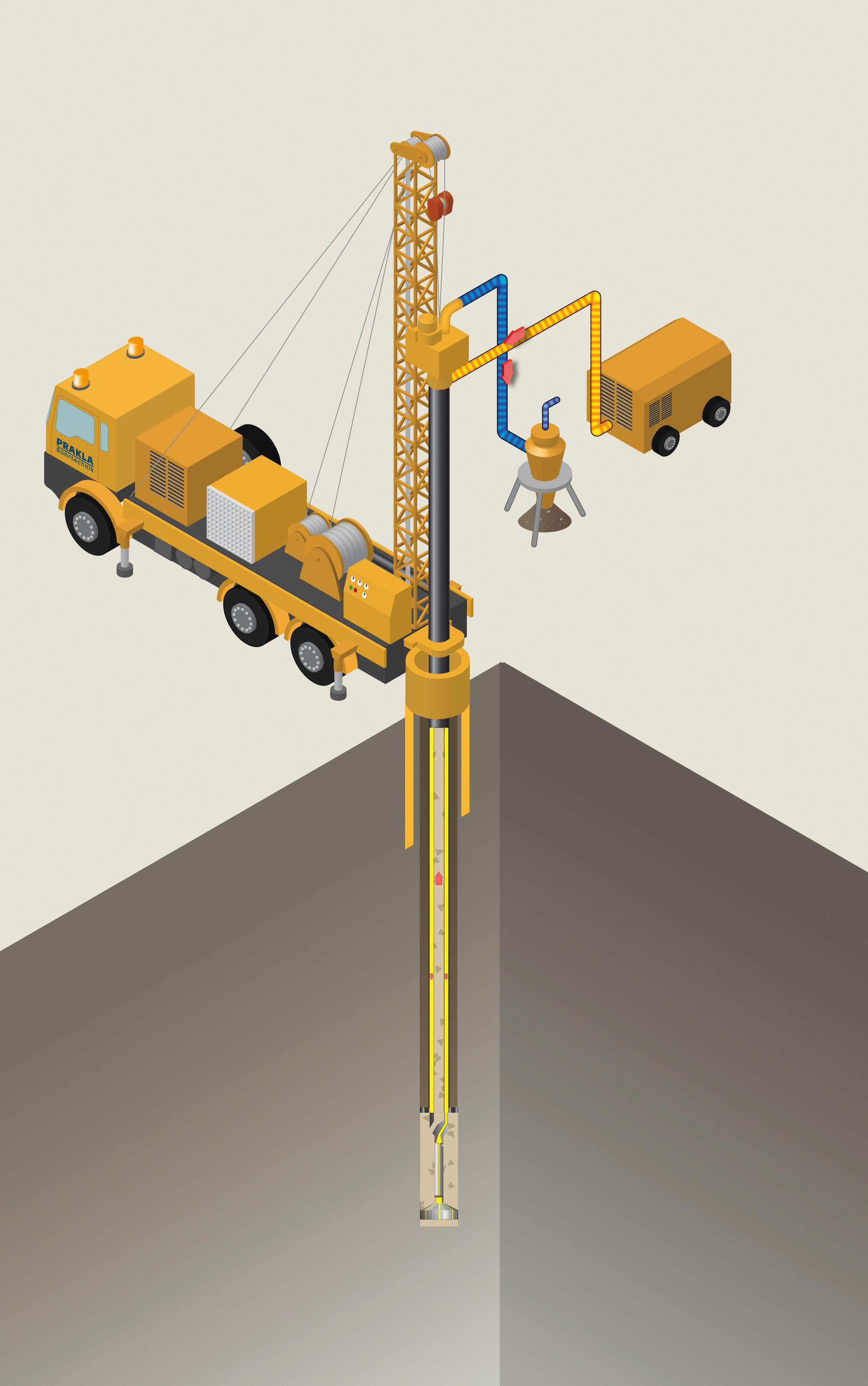
For down-the-hole hammer drilling, the drilling hammer is positioned in the bore hole. This is attached to the rotating drill string. The drilling hammer is driven by compressed air which is conveyed through the drill string to the hammer and also acts as a flushing agent. After leaving the drill spoil, the air transports the dissolved drill spoil in the angular gap above ground level. This method is primarily used for drilling in hard, firm rock in the area of well construction and mining, as well as in stone quarries. Down-the-hole hammer drilling can also be used with the reverse circulation method. This is particularly worthwhile for large drilling diameters in mining.
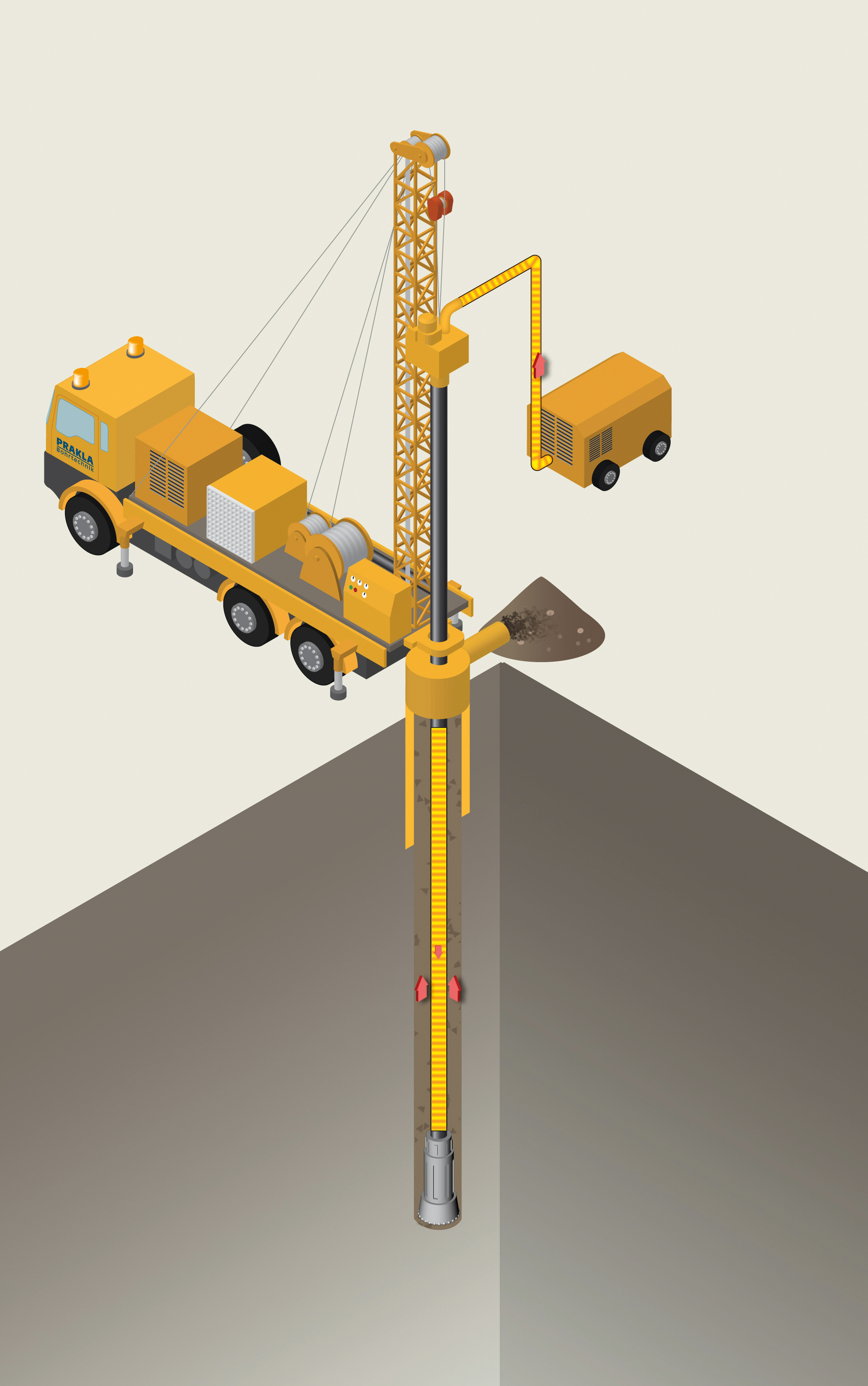
In the pressure flush drilling method, the water-based drilling fluid is pumped through the drill string into the bore hole and mixed with the drill spoil. The mixture is then transported upward in the annular gap between the drill string and the bore hole wall. After the separation of the drill spoil and drilling fluid, the flushing fluid flows back into the drill string. The pressure flush drilling method is applied for smaller drilling diameters (< 300 mm) in water well construction, mining, crude oil and natural gas drilling as well as for geothermal heat.
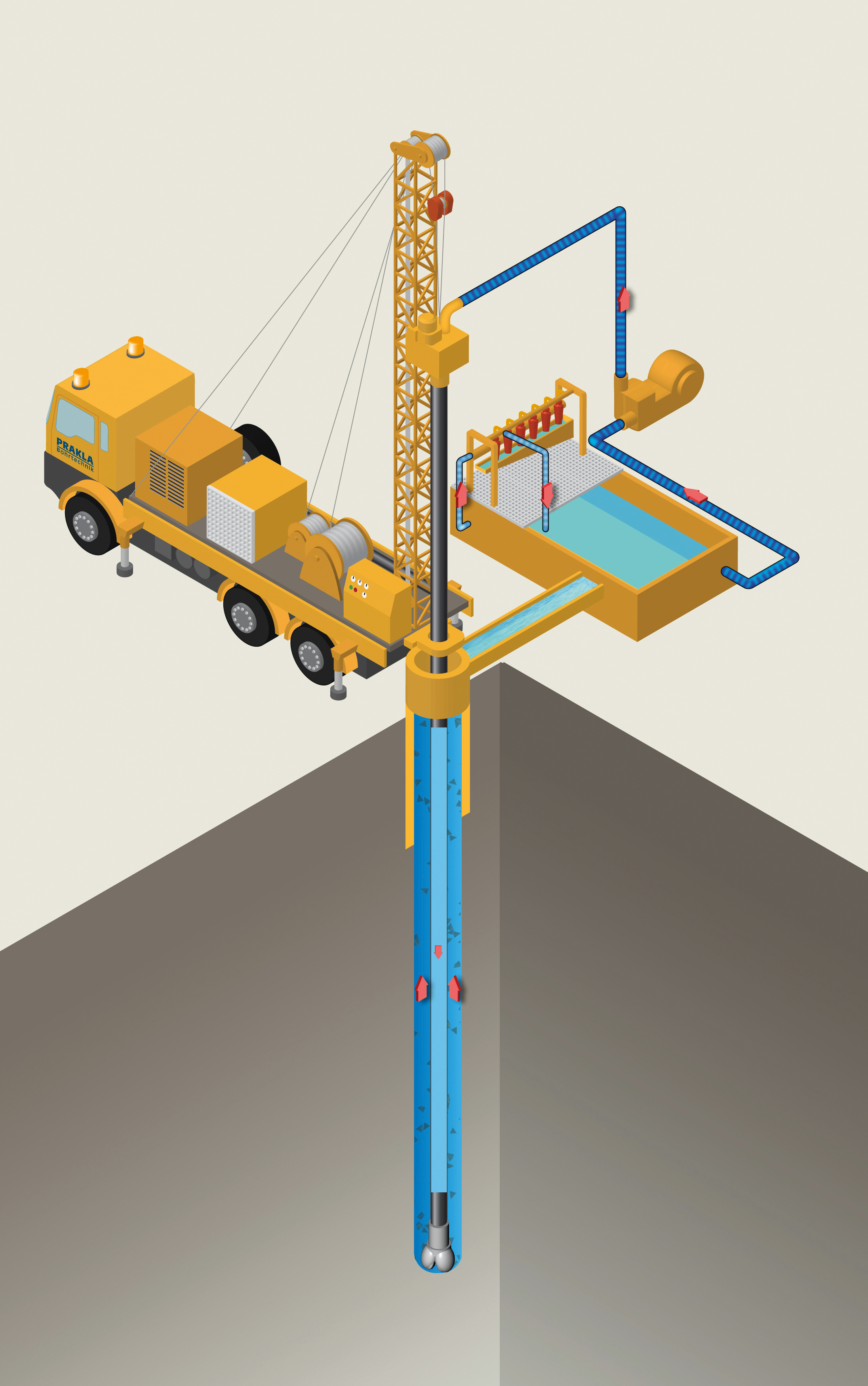
Downloads
Any questions?
I look forward to receiving your message or your call.
You might also be interested in:
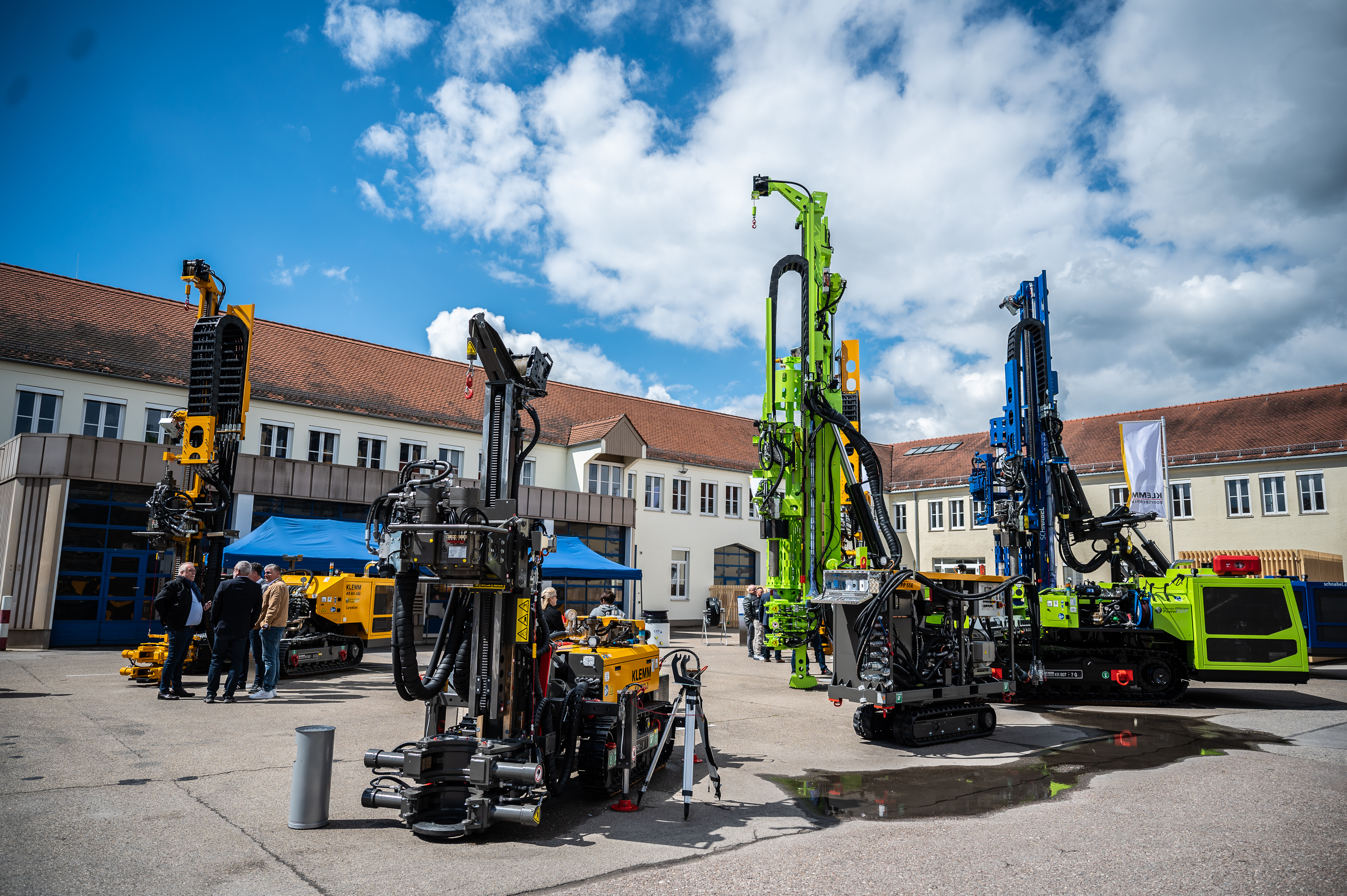
Whether anchor drilling, high pressure injection or geothermal heat: Discover the versatile KR series from KLEMM Bohrtechnik GmbH.
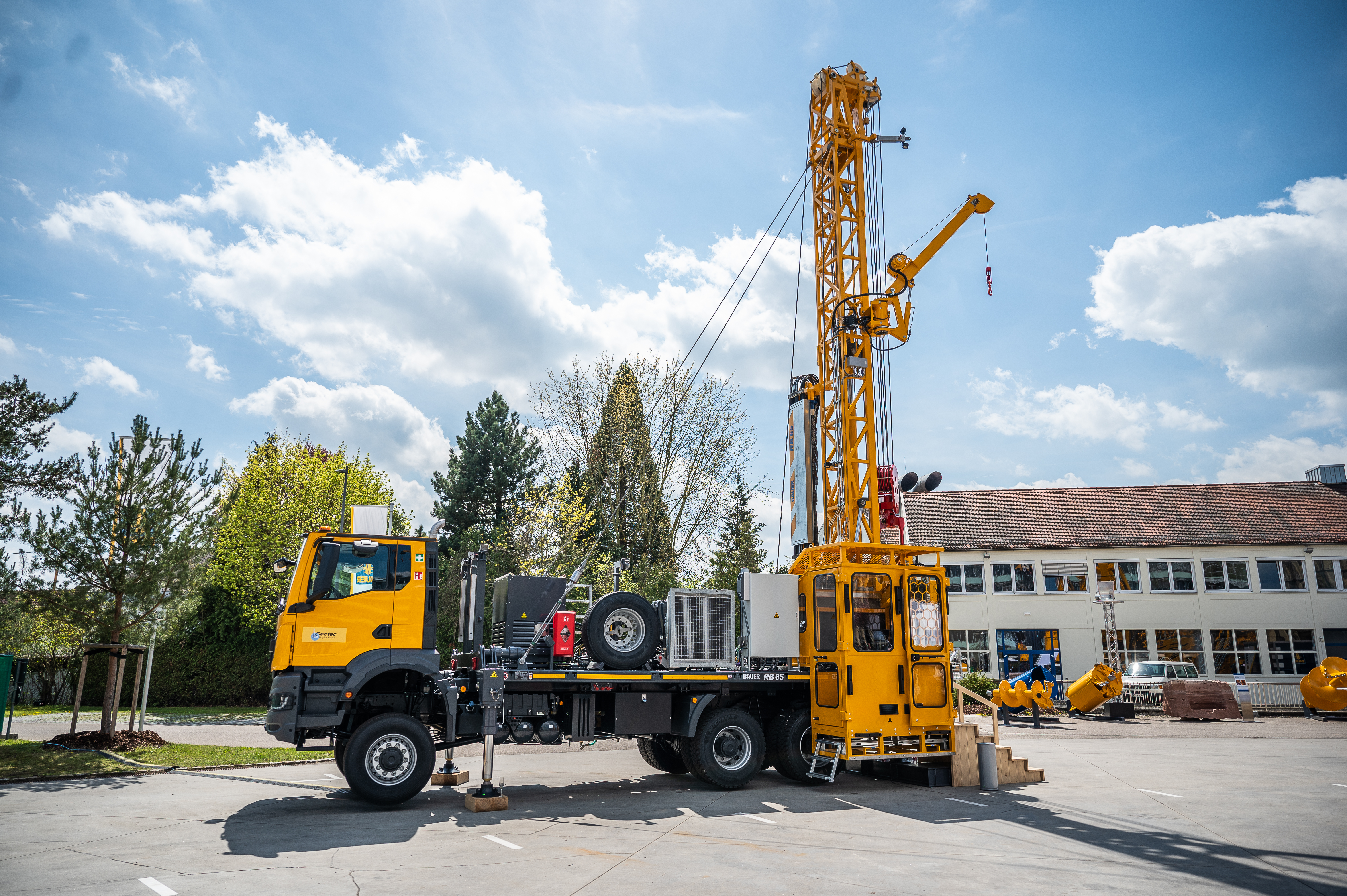
With our efficient rigs for water well construction, geothermal heat and exploration, you can stay mobile. Discover them now! We would be happy to advise you.
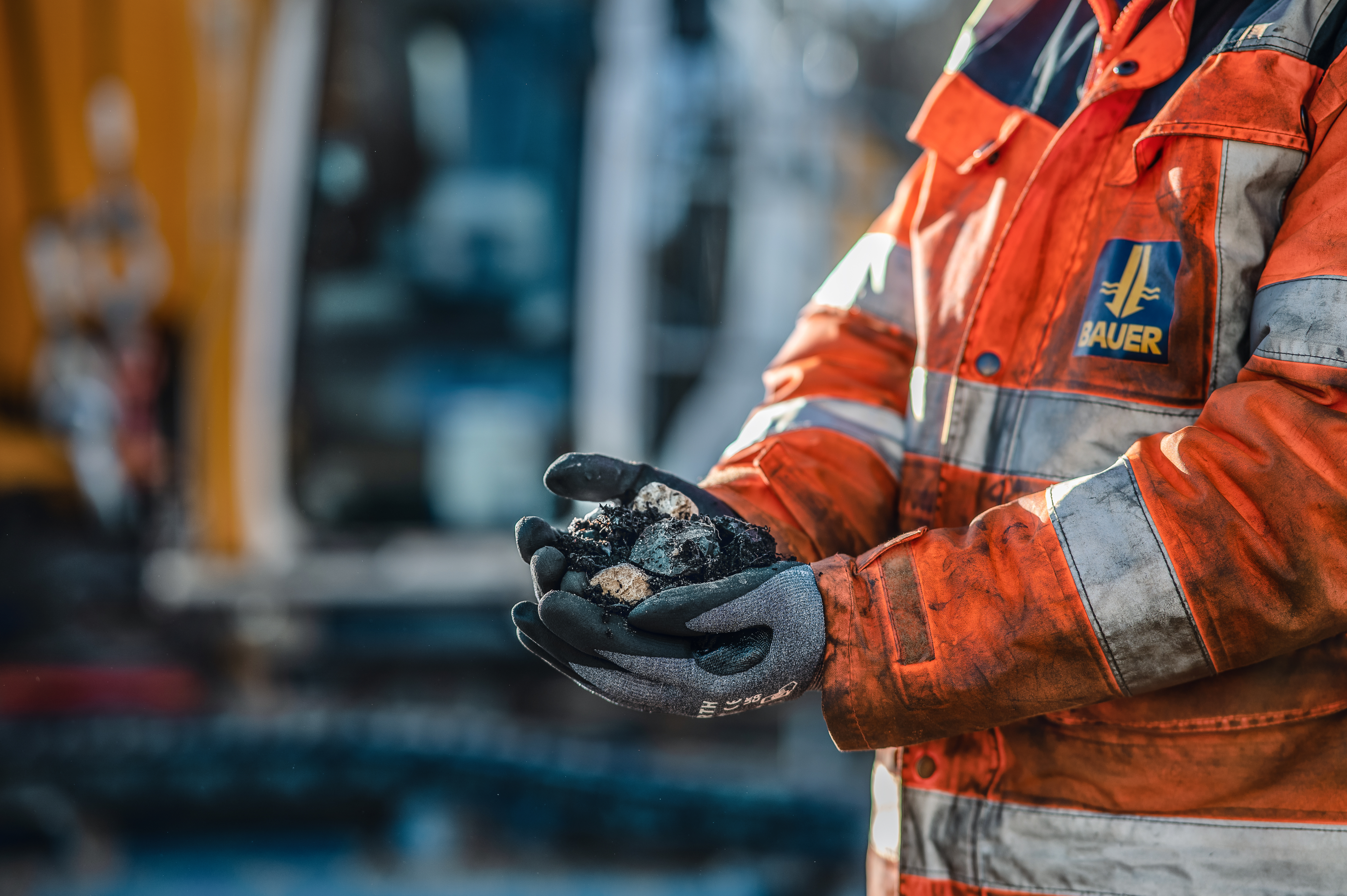
Whether drilling, impact driving, cutting, mixing or vibrating, the variety of specialist foundation engineering methods is impressive. An overview of the most common methods.
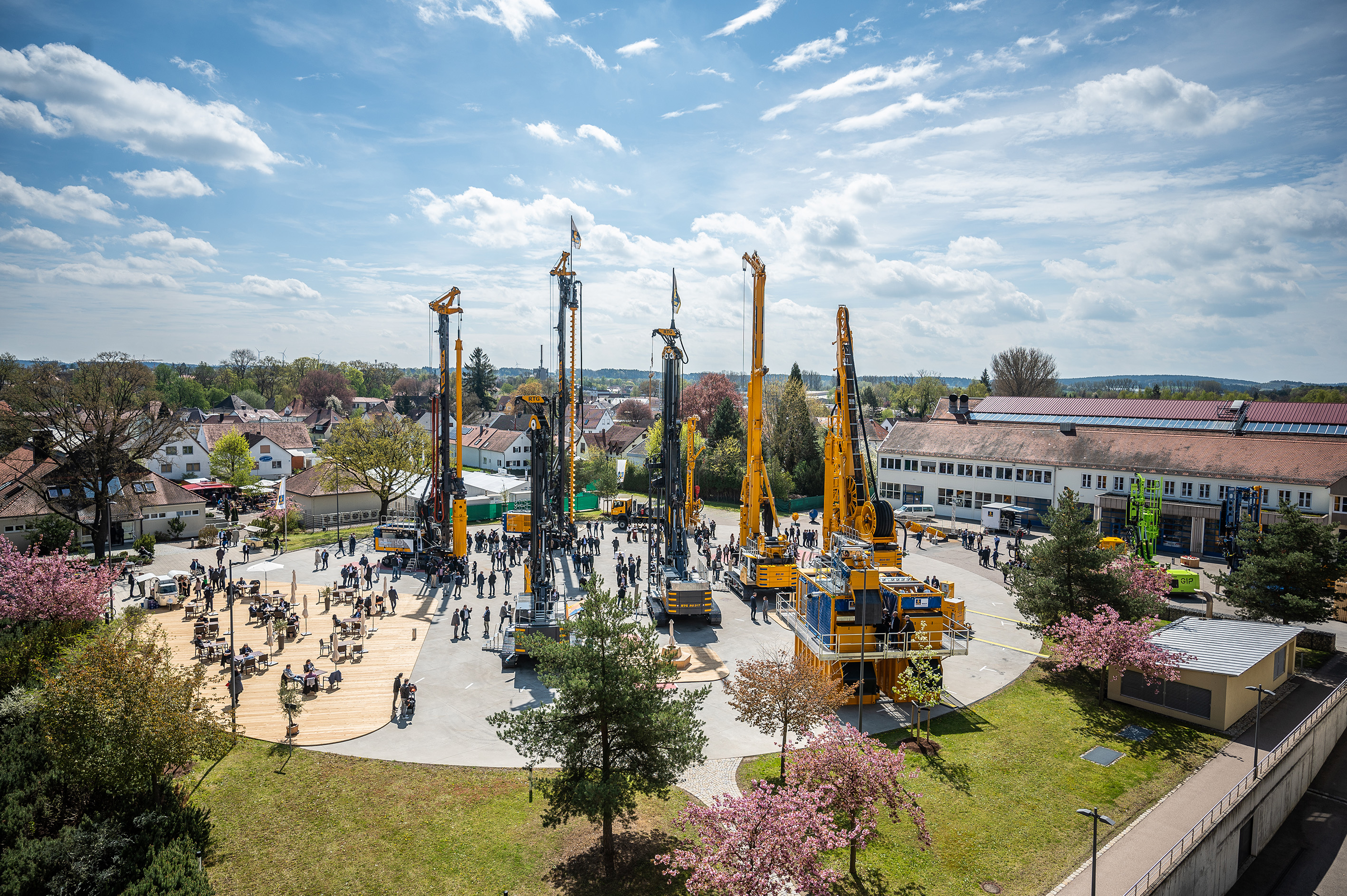
With our subsidiaries and branch offices, we offer complete solutions for specialist foundation engineering from a single source. Get to know our network!