In-house exhibition of the BAUER Maschinen Group: Enthusiastic guests and impressive exhibits
Schrobenhausen, Germany – After a break of five years, it was finally time again on April 27: The BAUER Maschinen Group welcomed roughly 1,500 guests from the region and all over Germany as well as international guests from more than 50 countries to the opening of its traditional in-house exhibition at their headquarters in Schrobenhausen. The slogan for this year’s event: be excited. “Whether for alternative drive systems, noise reduction initiatives, the latest developments in water well construction, revolutionary enhancements in diaphragm wall technology or equipment technology for the offshore segment, Bauer is a pioneer,” said Dr. Ruediger Kaub, Managing Director of BAUER Maschinen GmbH, in his opening speech. Jochen Grundmann, Board Member and Global Sales Director, emphasized: “Our outlook for the future is very positive. This is because we always see an opportunity in all of the major challenges faced by our business.”
On the premises in Schrobenhausen and the plant grounds in Aresing, guests were able to experience specialist foundation engineering technology first-hand for a total of four days. Alongside absolute innovations, an impressive mix from the Bauer product range was presented, starting with BG drilling rigs, drilling tools, well drilling rigs and MC duty-cycle cranes along with diaphragm wall technology, all the way to mixing and separation technology. Of course, KLEMM Bohrtechnik GmbH and RTG Rammtechnik GmbH participated again and presented their innovations. For numerous pieces of equipment, visitors were treated to an exciting glimpse “under the hood” at the world of alternative drive systems.
A range of drilling rigs
The smallest drilling rig on display, which “welcomed” visitors right at the entrance of the exhibit grounds, was the BG 20 H. With a transport width of just 2.5 m and a transport height of 3.3 m including power rotary head (KDK) and Kelly bar, the compact drilling rig is particularly impressive when it comes to transport and assembly on the construction site. With a sound power level of just 105 dB(A), the equipment operates very quietly. In line with this, the BG 20 H was displayed with a “Silent Bucket”, a drill bucket with sound-optimized design to reduce process noise – after all, the topic of noise and noise prevention is becoming increasingly important on sites.
With a BG 23 H, Bauer also displayed a versatile multi-function drilling rig including equipment for continuous flight auger drilling in the extended equipment configuration SPEX (Single Pass Extreme). This provides active vertical thrust forces over the entire feed length by means of the crowd winch system for drilling of compact soil strata. Despite its extremely compact unit size, the BG 23 H reaches a drilling depth of 25 m with a 7.1 m long special mast extension which can be folded hydraulically for transport using wireless controls. Optional assistance systems for fully automated drilling and concreting provide the operator with effective assistance and ensure continuous high pile quality.
Lots of attention was given to the eBG 33 H all electric, which Bauer first presented to a specialist audience at the Bauma in Munich in fall 2022. For this purely electrical multi-function drilling rig with a maximum system output of 420 kW, the diesel engine was replaced by a powerful electric drive. In addition, all significant main consumers such as the rotary head and main winch operate purely electrically with optimal efficiency. Thanks to the battery pack integrated into the machine, the eBG 33 H all electric can be used off-grid in typical Kelly load cycles for an entire shift. The machine operates highly efficiently with no local CO2 emissions, and achieves impressively low noise emission values. Equipment features include the latest version of the B-Tronic 5 control system, which elevates work with a Bauer drilling rig to a new level in terms of user-friendliness and data networking.
The BG 36 ValueLine, another model from an equipment series optimized for Kelly drilling, rounds off the BG range on the exhibition grounds in Schrobenhausen. The ValueLine concept enables longer masts and corresponding drilling depths as a result, while the equipment size remains the same. The long mast in the series optimized for Kelly drilling enables deeper drilling depths, while larger drilling diameters are achieved through an extended distance from the drilling axis.
Additional Bauer drilling rigs with a wide variety of tools and assistance systems – including the Stability Plus assistance package for considerably expanded yet fully monitored range of outreach – were also exhibited on the plant grounds in nearby Aresing. The exhibits here also included a complete system for the construction of stone columns using vibration drilling, the BF 15. The compact, user-friendly machine is equipped with features such as a B-APS positioning system, which allows each stone column to be manually approached with high precision. Visualization is provided on the B-Tronic work screen.
Groundbreaking diaphragm wall equipment
In the form of the BCS 185, Bauer presented a specialized cutter carrier that offers a highly economical entry-level variant for a cutter system combined with the hose drum system HDS 90-T. This equipment can achieve trench depths of up to 90 m. During the development process, one key focus was to ensure compact and modular design in order to optimize the equipment for assembly and transport to site. When assembled, the BCS 185 is thus particularly suited for operation on sites with tight space constraints. The exhibited machine is a holistic concept that elevates the area of diaphragm wall equipment to a new level in terms of functionality. The equipment will soon be used on a cutter project in the French city of Toulouse.
As a special treat, the guests on the plant grounds in Aresing were able to witness a GB 50 Low Headroom live in action. Tight space constraints with a working height of 6 m are no problem for this hydraulic grab carrier. It is capable of installing cut-off walls with widths between 800 and 1,200 mm up to a depth of 50 m. After the exhibition, this equipment also embarked on a journey to London, where it will show off all its advantages on a construction site for the HS2 infrastructure project.
Innovative drilling attachment for MC duty-cycle crane
The robust MC 96 from Bauer is characterized, like all duty-cycle cranes from the MC series, by its versatile applications. For the first time, the MC 96 was now presented with a new drilling attachment, the Super Reach Attachment 400 (SRA 400), which is capable of drilling with an excellent work radius of up to 13 m. This adds an innovative option to the applications of the MC duty-cycle crane. The drill technology of the SRA 400 is based on standard components of Bauer drilling rigs and offers full integration into the control system of the MC, including the use of established assistance systems.
The Smart Grab Control newly developed by Bauer represents a quantum leap in the operation of duty-cycle cranes with free-fall winches. This system, available for all MC models and patent-pending, makes it possible for the first time to operate a rope grab with the same speed that many operators know from diaphragm wall hydraulic grabs. The previous highly demanding process of moving the free-fall brakes and couplings of the two main winches with hydraulic foot pedals becomes unnecessary when using this system. The operator can fully control all grab functions by using the joysticks combined with several integrated controls and buttons.
Mobile drilling rigs – flexible down to the smallest details
Bauer offers mobile drilling rigs of various kinds for the development of drinking water sources, as well as for raw material exploration, geothermal heat and mining operation. They all have one thing in common: Where large drilling depths or drilling diameters have to be achieved, the universal rigs in the RB series offer optimal technical prerequisites for successful drilling work. As an example for mobile drilling rigs, Bauer exhibited the RB 65. This rig can be used to excavate boreholes up to 1,550 m (depending on the size and weight of the drilling tool as well as the geology). An electrical pilot control is installed in the RB 65 in order to use the equipment more economically and safely with the help of automation processes. Another bonus point: Due to its modular design, the equipment of the rig can be adapted easily to the specific requirements, making it flexible down to the smallest details.
Exciting impact driving technology
RTG Rammtechnik GmbH exhibited its RG 19 T hybrid and the RG 21 T. As the first hybrid model in the telescoping leader segment, the RG 19 T is setting standards with its considerable reduction of CO2 and noise emissions by up to 50%. Demand-specific power control shared between the electric drive and diesel engine ensures an optimal use of these two drive types. Where the power demand is low, electric hydraulic operation is possible. The SilentVibro package, sheet pile assistant and Operate remote control are just several features that increase occupational safety and productivity.
The RG 21 T, a proven and versatile telescopic leader, was presented with a newly developed system for soil mixing, the Multi Shaft MixingMSM with Automatic Coupling System (ACS). The coupling system enables rapid changes between the RG attachment units and the MSM. The equipment is characterized by its excellent versatility: Not only is it available for different drilling axes, it can also operate up to four drill strings at the same time, so it can be used for Double Column Mixing, Triple Column Mixing or Quad Column Mixing. Furthermore, the Operate remote control was presented on an RG 16 T, which can be used to operate all functions.
The latest generation of geothermal equipment and anchor drilling rigs
KLEMM Bohrtechnik GmbH presented several powerful anchor drilling rigs in various power classes; extremely compact drilling rigs with variable kinematics including an energy-efficient geothermal drilling rig with excellent drilling performance.
The KR 702-3 is the latest development in the widely used KR 702 series for specialist foundation engineering applications involving tight space constraints. The already established technical advantages of the previous version have been enhanced with added features, in particular the new hydraulic and electric controls. Power-optimized PowerSharing is now possible with both of the available power packs PP 55E and PP 117G. The “intelligent” connection with the PP 117G offers EEP functionality for the first time. As well as many small improvements, the drilling rig now also comes with a new wireless remote control.
The KR 801 series is in a league of its own for especially compact universal drilling rigs. With a 2,200 mm wide pendulum-type crawler, the KR 801-3GS drilling rig is optimally suited for nearly all work involved in specialist foundation engineering, from easy to more complex drilling tasks. One particular focus is on enhancement, with greater engine performance and a higher flow rate in the pumps.
With the KR 805-3GW, a powerful rig for probe drilling for near-surface geothermal heat extraction, it’s possible to reach drilling depths of up to 375 m using the double-head drilling method. Weighing almost 20 tons, this rig includes a crane, a drill string manipulator, and a hydraulic recovery and pulling device.
The anchor drilling rig KR 806-4GM with on-board revolver drum and manipulator MAG Type 6.1 for double drill strings is characterized by its high drilling performance and compact dimensions. Using the powertrain of the KR 806-3GS, it was developed to be handled by one person to carry out difficult overburden drilling tasks using the double-head system. The kinematics system is primarily designed for low-angle inclined drilling with deep drilling starter points. The pile borings can also be drilled with drilling starter points next to the chassis.
The crawler-based drilling rig KR 807-7G with a 245 kW power drive is the most powerful drilling rig in the KLEMM Bohrtechnik GmbH portfolio. The engine complies with current exhaust emission standards EU Tier V and EPA Tier 4f. This large and particularly robust universal and anchor drilling rig is designed for numerous uses within specialist foundation engineering and in other areas of application. With the patented on-board revolver drum and manipulator Type MAG 7.0 for double drill strings, the equipment is in a league of its own.
All the equipment exhibited offers smart features, such as the KLEMM developed and patented PowerSharing, and the Energy Efficiency Package (EEP) – now integrated as a standard. These smart features assist the user in both economically and ecologically optimizing their jobsites, for example through significantly reduced fuel consumption and lower pollutants and noise emissions.
Mixing and separation technology
Bauer MAT Slurry Handling Systems is the specialist in the BAUER Maschinen Group when it comes to mixing and separation technology. At Bauer’s in-house exhibition, this branch from Allgäu presented a new desanding plant with the BE 600-C that truly keeps it all together: This two-stage equipment with double cyclone design is installed within a container frame. Apart from its throughput rate of 600 m3 per hour, the plant is impressively fast and easy to assemble, so it can be put into operation in next to no time for cutting, tunneling, grabbing or drilling projects. What makes it unique: As needed, the BE 600-C can be divided into two individual BE 300-C units, and the upstream coarse screen can also feed just a single unit.
Alongside the large BE 600-C unit, two new compact Obermann MAT products were exhibited: The fully automated AVS 110-E model grouting station is not only a fully electrical solution for grouting and follow-up injection of anchors and micropiles: it also enables automatic data recording of pressure and flow rate volumes. The DP 63-J with its two upright plunger pumps is predestined for use in flush drilling, follow-up improvements and injections. Here as well, the optional PQ controls enable recording of pressure and flow rate volumes. Together with the KLEMM drilling rigs, the Obermann MAT equipment makes an ideal product range for various applications in specialist foundation engineering.
A perfect combination of equipment technology and stimulating conversation
In Bauer’s Old Welding Shop – formerly a production facility, now an event location with industrial charm – guests were able to inform themselves about digital solutions and topics related to sustainability. The topic areas of water, energy and mining, maritime technologies, parts and services along with the BAUER Training Center, Spantec and the GWE Group were also exhibited there. At the topic stands, visitors had many opportunities to engage in dialog with the specialist departments. Daily live presentations in Aresing and the supporting program in the evenings with lots of Bavarian charm also helped to ensure that the first Bauer in-house exhibition after the COVID-19 break was an unforgettable experience.
Your Contact
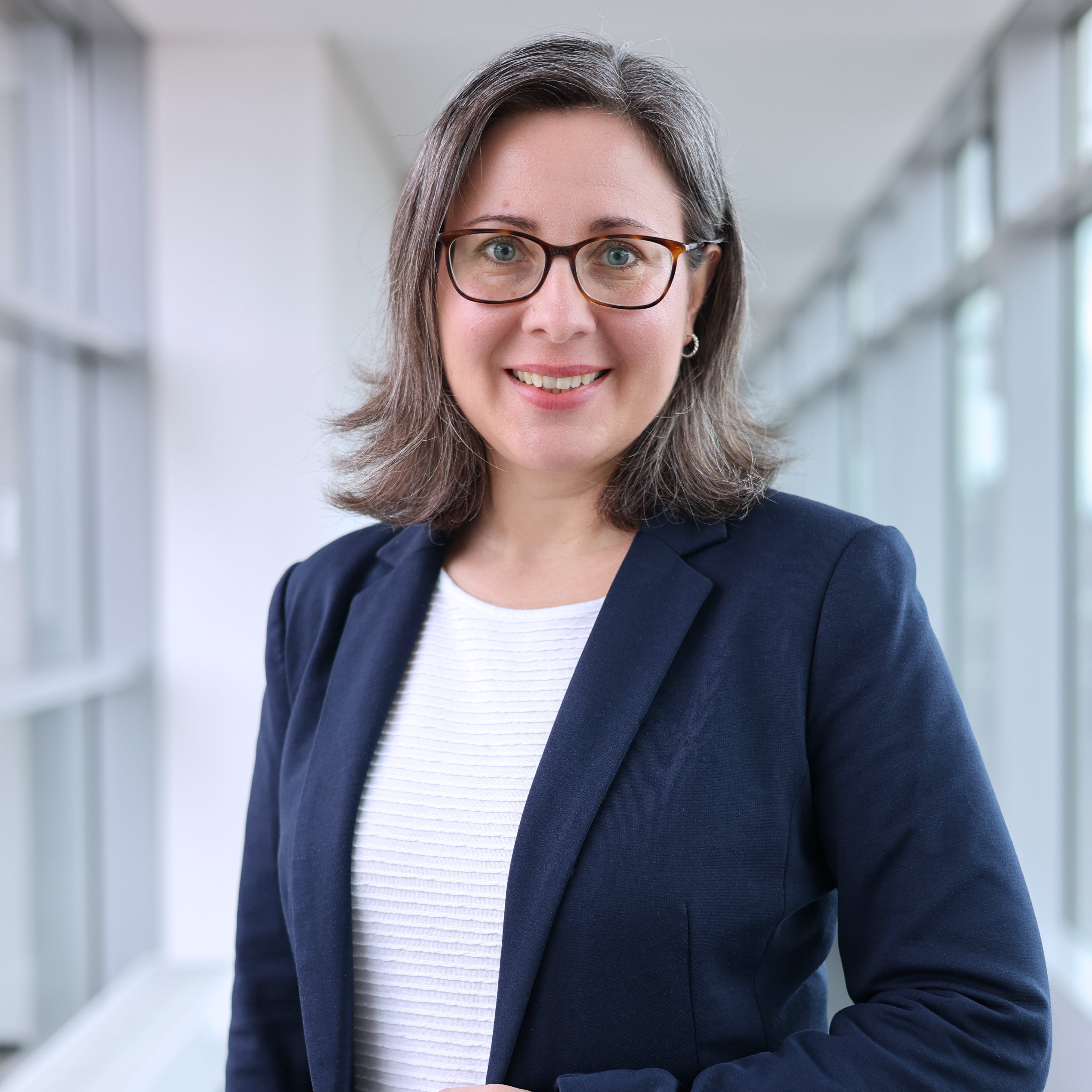
Specialized press Equipment, regional press, HR press